Introduction
This project started as a Strategic Advisory Services consulting engagement, but then moved into External Project Management by managing a seasoned IT development team to deliver the solution that was proposed. Normerica Inc., recently purchased by Minerals Technologies, reached out to us with an urgent need to streamline their logistics and supply chain operations by automating internal processes.
To reveal the challenges and present the solution, we compiled a detailed approach and analyzed the aspects as follows:
- Current state analysis: We studied and documented the operations of Customer Service Relations (CSRs) and Logistics departments and conducted the analysis of the employees’ feedback.
- Key business processes determination: We outlined areas for improvement, which were data management and accuracy, order fulfilment lifecycle, reporting automation, and inventory management.
- Solutions examination: We examined the leading digital systems and offered the implementation of the most compatible technology.
Challenges
Prior to the start of this study, we made several initial assumptions:
- Employees are overburdened with highly repetitive tasks.
- Departments lack communication with each other.
- Logistical problems arise due to the low availability of required information.
Further we tested the above assumptions in 3 independent stages:
- Employees were approached with several specific requests - to explain the most routine daily process, to describe the most time-consuming part of their days, and to name something that made them frustrated on a regular basis.
- The daily tasks that were identified as time-consuming by the employees were timed to verify the validity of the claims made.
- A Service Blueprint of the current fulfillment lifecycle was created, in order to clearly identify the roles that the departments play and further test the initial assumptions.
Normerica Inc. faced several challenges in their previous practices, leading to inefficiencies and operational difficulties. These issues motivated the organization to seek significant changes to improve overall efficiency and productivity.
Having tested a line of assumptions, the following aggravating issues were identified:
- Employee Morale: Low morale due to simple, repetitive tasks being manual.
- Software Issues: Frequent freezing of Microsoft Office programs, causing users to wait before they could start working.
- Data Accessibility: Difficulty accessing data immediately due to long load times of the existing ERP (Enterprise Resource Planning) system which often took 15 minutes to load all the data.
- Reporting Burden: Management relied heavily on employees for report creation due to inability to generate reports and view data in real-time.
- Role Dispersion: Roles dispersed among multiple departments (e.g., buyers, logistics associates, and CSRs) reduced individual departmental efficiency due to their heavy daily routine burden.
The findings confirmed that employees spent a large amount of time on tasks that could be automated, such as reporting, manual data processing, and communication. The figure below represents the average daily time allocation per logistics associate based on our research:
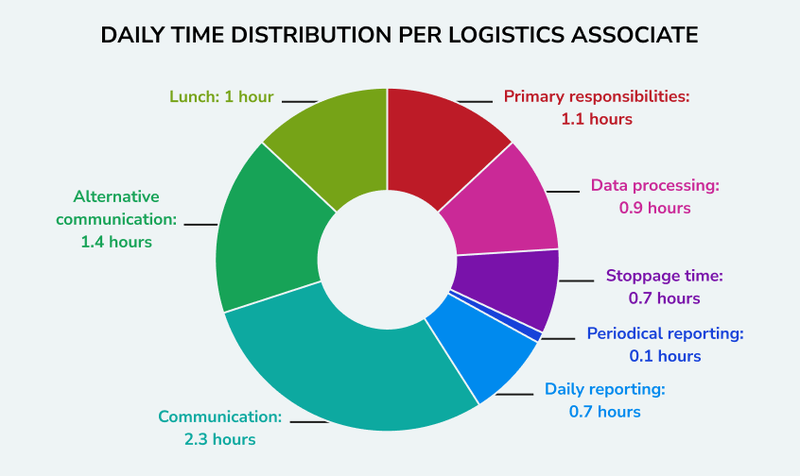
Solution
Given the constraints and limitations set by the client, there was no solution on the market that met their needs exactly. Their requirements included keeping their server with all the data in-house, which created the need to integrate with the existing data, while ensuring that their existing systems would not be overwhelmed.
To address the identified challenges within the constraints and limitations, we implemented a comprehensive solution leveraging Microsoft’s technology stack, hosted on Microsoft Azure.
We decided to utilize two databases - SQL Server for transactional data and Mongo DB for historical data. The frontend was built following the SPA (Single-Page Application) model, which was the best practice in the development of similar systems at that moment.
To pull data at pre-determined time intervals and write information back via declared touch points we decided to integrate with the in-house Oracle database, enabling automated synchronization. To display the orders for the employees to work on, we created a Kanban board.
As a result, we provided a solution to address the challenges:
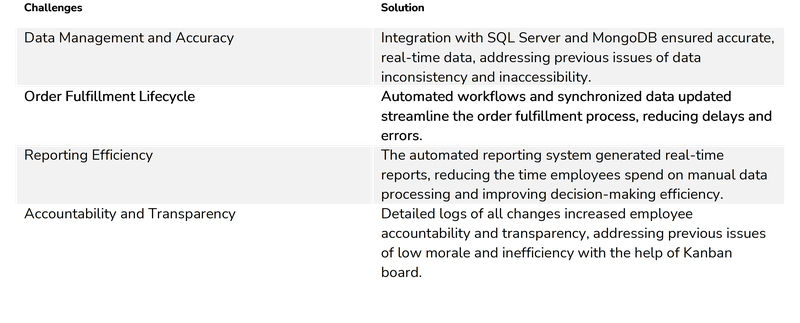
Implementation
To implement the new system, we leveraged Microsoft’s technology stack, hosted on Microsoft Azure, ensuring scalability, security, and reliability.
System architecture: It included SQL Server for managing transactional data and MongoDB for tracking historical data, logging changes with detailed user information to increase accountability.
Frontend Development: The frontend was developed as a Single-Page Application (SPA), providing a seamless and responsive user experience.
Integration and Data Synchronization: The system was integrated with the existing Oracle database. Data is pulled at pre-determined intervals, and information is written back via declared touchpoints. Automatic synchronization ensures any modifications in the Oracle database are reflected in the new system, maintaining data integrity by updating only necessary fields.
Efficiency and Load Management: The new implementation introduced minimal additional load on the existing database while centralizing data requests. This reduced the load on the current database by maintaining up-to-date data accessible based on user roles, enhancing overall efficiency.
Outcome
As a result of the solution implementation, the following processes were automated and operate in the following ways:
- Order Creation: CSRs create orders and set delivery dates within the new system.
- Shipping Tender: The system automatically generates and sends tenders to the top carrier via email, determined by analyzing historical data. Carriers can respond via a link to accept, counter, or decline the offer.
- Tender Outcome: Accepted tenders move to the logistics department for ETA monitoring, with automatic email updates. Rejected tenders trigger automated emails to other carriers for new offers.
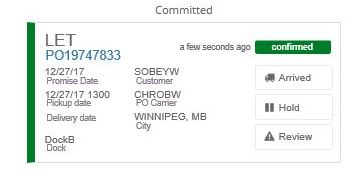
- Carrier Commitment: Once a carrier is found, the load moves to the Committed state for ETA monitoring.
- Warehouse Visibility: Orders appear on the Warehouse’s Kanban board with buttons (Arrived, Docked, Departed) logging user actions.
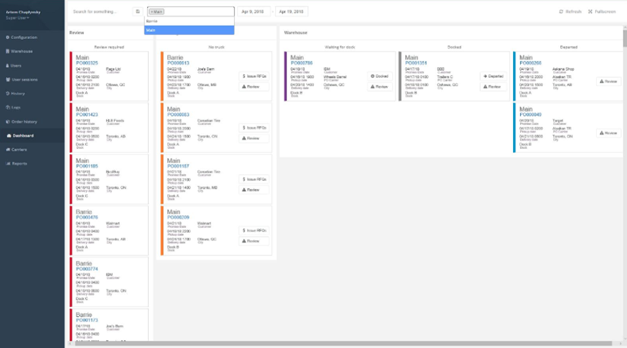
- Order Synchronization: Shipped orders are synchronized with the Oracle system, updating the database with carrier and shipment details.
- Carrier Activity Recording: All carrier actions are logged for analytics and reporting, improving carrier reliability assessments.
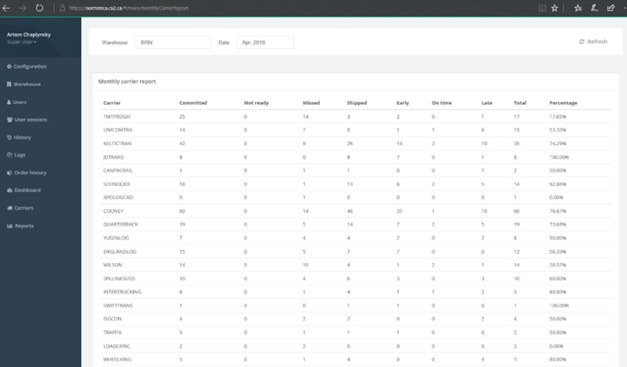
Results
The implementation of the solution we devised optimized operations at Normerica Inc., helping their internal systems, reducing the load on their server and giving their logistics associates and CSRs a way to do their work in a different environment, which saved them a lot of time. Even though the organization has significantly changed since the solution was implemented, it was a great step forward at that time.
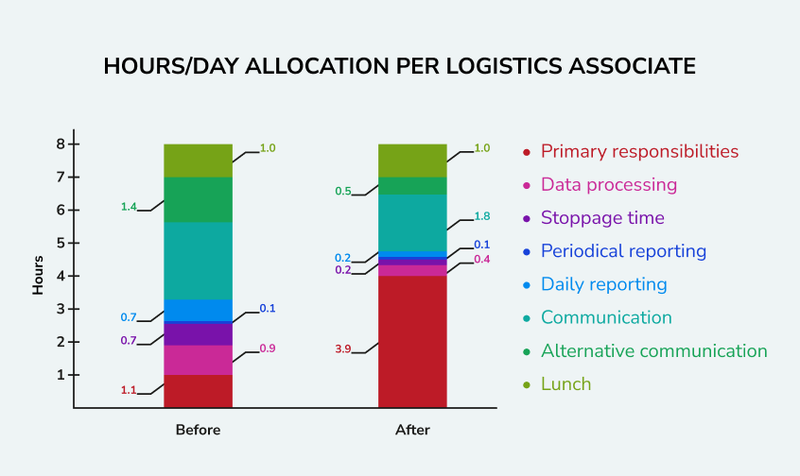
The system development project was completed, and recommendations were provided, such as transferring system functionalities to the CSR (Customer Service Relations) Department and expanding the functionality to further improve operations. Furthermore, a number of additional automation opportunities were identified. Finally, additional management reports were defined and developed for implementation to give executives the data they need for decision-making.